The State of the Technical Textile Supply Chain in 2023
Company News, International StandardsJan 30, 2023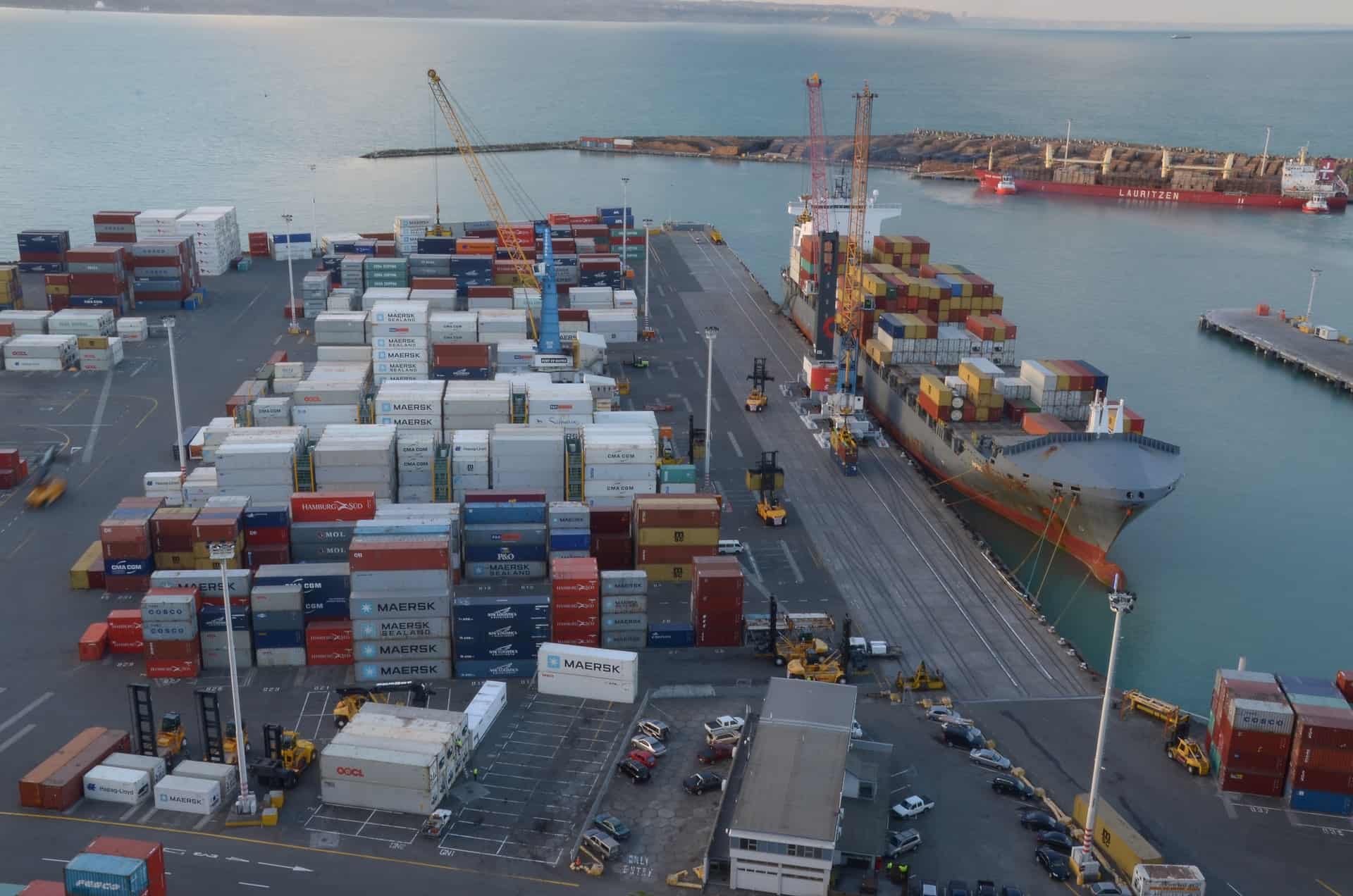
The Technical Textile Supply Chain in 2023
As a leading supplier of technical textiles for a wide range of applications, we have the unique opportunity to observe ongoing trends and shifts in the industry.
From medical equipment and marine safety applications to inflatable boats and flexible storage tanks, we provide essential products that serve as the driving material for these industries.
It was in 2021 that we first wrote about the state of the textile supply chain due to the series of destabilizing events that occurred one after another that challenged the industry.
Looking Back at The Supply Chain Instability of 2021
To begin, let’s summarize those events:
Covid-19
The Covid-19 pandemic has caused massive disruption to global trade, resulting in shortages of raw materials, production delays, and higher costs. This instability has had a significant impact on the industry, with many companies struggling to keep up with demand and maintain their supply chains.
The Texas Freeze
The Texas Freeze of 2021 was a devastating event that had a major impact on the technical textile supply chain. The unprecedented cold snap caused temperatures to drop below freezing for several days, resulting in widespread power outages and infrastructure damage across the state.
It took several weeks after the freeze for many polymer plants and facilities in and around Texas to return to operation. This was particularly problematic as Texas produces a substantial percentage of polymers in the United States, which are essential building blocks for many technical textile solutions. The sudden closure of these raw material production sites caused an immediate shortage, exacerbating the already high demand for these materials.
The disruption to production caused by the Texas freeze was felt across the entire industry.
The Suez Canal Jam
In March 2021, the Suez Canal was blocked for nearly a week due to a massive container ship running aground. This event had a major impact on the global supply chain, particularly in the technical textile sector. The Suez Canal is one of the most important shipping routes in the world and is used to transport goods from Asia to Europe and North America.
The Technical Textile Supply Chain in 2023
In 2022, the global supply chain began its recovery from the above events. Just as the industry began to enjoy the illusion of stability, the Ukraine-Russia war broke.
The conflict between Ukraine and Russia has swept across the globe, bringing about a wave of tensions and uncertainty not only in the political arena but also on the global economy.
While the energy sector has been drastically affected by the conflict— resulting in increased inflation, spiking costs for raw materials, and higher operational expenses—the direct disruption to the textile industry appears to be minimal.
A consumer-facing market, however, has historically felt the pressure first in times of an unstable economy. Especially those used for leisure, such as inflatable boats.
We are watching the rise in interest rates and how they will affect the global economy in 2023, as well as the prospect of a recession. As of now, the industry seems to have made a complete recovery and is relatively stable.
The Erez Approach to Facing Supply Chain Instability in 2023
Starting from material selection, customized solutions, production expertise or supply chain guidance, Erez strives to be a true partner that is more than just another supplier.
By being mindful of trends and shifts in the market, we have been able to deliver exceptional customer service with a commitment to excellence as a priority.
As we observe trends across these industries, we can adjust our strategies accordingly to help our partners succeed.
Share this Post