The Crucial Role of Oil Spill Containment Boom in Marine Pollution Cleanup
Environmental Control, Marine Safety, Sustainability, WeldingJun 17, 2024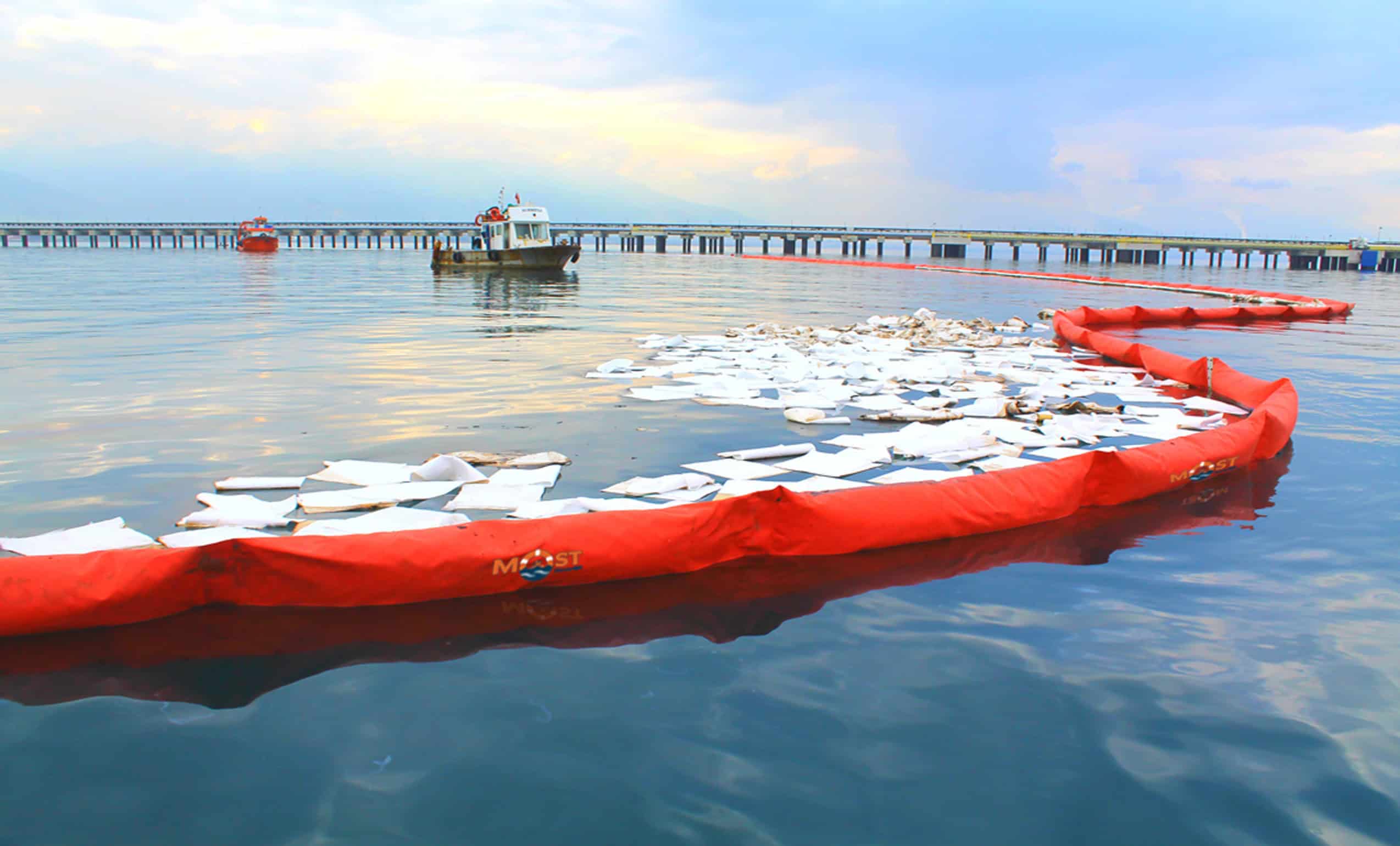
Ocean oil spills represent a major global environmental problem, devastatingly harming ecosystems. A Swift and effective response to these spills, by ensuring timely oil clean-up, is critically significant due to the severe risk of enduring long-term contamination associated with marine oil pollution in water bodies. In many past incidents, deploying an oil spill clean-up boom is one of the best solutions for cleaning up oil spills. These durable, high-strength barriers contain and control oil during a spill. In this aspect, the materials used to construct oil spill containment booms are crucial in mitigating such disasters.
Erez Textile provides highly effective and durable materials for crafting sturdy and durable oil booms. These materials have been used in marine oil clean-ups for years and have proven to be instrumental in combating oil spills worldwide.
Unraveling the Efficiency of Oil booms
Oil or spill containment booms are primarily used to contain and manage marine oil spills. These structures, built using high-quality and durable materials, effectively absorb spills, making the cleanup process faster and more manageable. Booms are available in different sizes based on the requirements.
Oil boom containment structures are designed to function effectively in various water environments, including tranquil, flowing, and open water territories. Oil boom manufacturers usually provide the product in sections that can be connected to achieve the necessary length for specific locations.
Their design is similar to silt barriers and consists of a top floatation mechanism, a bottom skirt, and a ballast chain to ensure stable positioning during deployment. To ensure reliable oil containment, these booms are usually compliant with the standards of the Environmental Protection Agency (EPA).
Permanent Booms vs Deployable Booms
Permanent and deployable oil booms are both vital tools in oil spill management but are used differently. Permanent booms with robust materials ensure continuous containment in high-risk areas prone to regular oil discharges, like oil rigs or refineries. Deployable booms are lightweight and designed for quick, temporary responses to unexpected oil spills. Each is essential—permanent booms for ongoing, preventative measures and deployable booms for emergency, reactive scenarios.
What materials are used for the outer shell of the boom?
Oil spill containment booms often comprise several materials that enhance their ability to contain and control oil spills effectively.
The main components in oil spill containment boom usually include PVC, TPU (Thermoplastic polyurethane), or synthetic rubber. These are the most common materials used for the outer shell of the boom due to their durability and resistance to oil and water. Oil boom manufacturers will choose the specific product according to their specifications, regulations, and designer requests.
Key Features of Deployable Oil Booms: A Quick Guide
When it comes to deployable oil booms, understanding their key features is integral. These include:
- Rapid and Easy Deployment: Their design allows for quick setting up, crucial during emergency spill responses.
- Single Point Inflation: This simplifies and accelerates the setup process.
- Internal Bulkhead: This provides added strength and durability.
- Durable Outer Shell: The boom’s structure, made from resilient and flexible TPU (Thermoplastic polyurethane), can withstand challenging conditions.
- Quick Coverage: The ability to rapidly deploy many meters of boom in mere minutes ensures extensive coverage.
- Fast and Safe Deployment: Safety isn’t compromised for speed during deployment.
- Excellent Wave Following: Their fabric flexibility and low inflation pressure enable them to follow wave movements closely, effectively containing oil even in choppy waters.
- High Integrity: These booms boast a high level of structural integrity, contributing to effective performance.
- Wide Temperature Range: Their ability to operate in a broad temperature range, from -40ºC to +90ºC, renders them versatile for varied climate conditions.
Erez Textile’s Role in Oil Spill Containment Boom Manufacturing
Erez Textile is an expert in producing advanced technical textiles globally. These materials excel as key components in oil spill containment equipment. Keeping in mind the main factor in oil clean-up projects, which is the urgency of containing oil spill incidents, Erez develops materials designed to be used in products that are quick to deploy and resist harsh conditions, coupling durability with cost-effectiveness.
Erez offers a diversified range of materials tailored to various oil boom requirements.
- ECOAT™ – This is used for lightweight booms filled with foam, which are ideal for small marinas.
- REZCOAT™ – From mid to large-size booms,
- ERCOAT™ – This is used for medium-sized inflatable booms.
Research indicates that quickly deploying and using oil booms can reduce the amount of oil reaching affected areas by up to 95 percent, significantly limiting environmental damage.
Oil Spill Containment Boom at Work: Major Oil Spills in Recent Decades
Oil booms have been crucial in managing some of the most notorious oil spills in recent history.
- Deepwater Horizon Spill:
One of the largest marine oil spills in history occurred in the Gulf of Mexico in 2010. The Deepwater Horizon spill had a disastrous impact on the local ecosystems. Oil booms played a pivotal role in containing the spill, absorbing large quantities of oil and significantly contributing to the clean-up operations.
- Kalamazoo River Spill:
In 2010, a pipeline leak led to a massive oil spill in the Kalamazoo River, Michigan. The oil spill spread over 38 miles, and the cleanup took five years to complete. Once again, oil booms were used extensively in the cleanup process to contain and absorb oil from the river.
- Morris J. Berman Spill:
On January 7, 1994, the Morris J. Berman, a single-hull barge, collided with a coral reef near San Juan, Puerto Rico, leading to a catastrophic spill of 750,000 gallons of heavy-grade oil. This spill affected tourism, fishing industries, and wildlife along the shores of Puerto Rico, Isla de Culebra, and Isla de Vieques, having long-lasting impacts on the biological and natural resources of the entire Puerto Rican area. The cleanup process required extensive efforts, and oil booms played a significant role in this operation, aiding in containment and absorption of the oil.
Custom Material Solutions for Oil Boom Construction at Erez
Erez Textile is equipped with a sophisticated laboratory that is fully equipped with all the necessary equipment for stringent testing, ensuring that our materials meet the required performance standards. Our team of experts excels in creating tailor-made combinations of diverse synthetic fabrics and materials. This means we can customize oil boom materials that deliver superior performance at a cost significantly lower than conventional methods. At Erez, we guide you towards identifying the ideal material for constructing your oil booms. We do this by thoroughly understanding the unique application requirements and providing materials that meet the performance standards without exceeding the budget constraints.
Why Choose Erez for Your Next Oil Boom Design
Beyond our commitment to producing quality materials, our true strength lies in our dedication to understanding our client’s unique application requirements. We work with you to pinpoint the appropriate materials for your oil boom and develop a product tailored to your needs. When you work with us, we find the optimal material tailored to your budget. Our experts test and certify your oil boom materials to ensure they meet stringent standards. We provide insights to optimize your manufacturing procedure to reduce costs.
Share this Post